From the moment internal combustion engines were invented, balancing proved to be a top concern. Part breaks signalled important troubles for manufacturers, not to mention vibrations produced by inertia pressures and gas combustion.
The mobile parts of an engine are submitted to acceleration and deceleration phases that are particularly violent considering their mass and inertia. That's why engineers have to factor in static balancing (idling body) and dynamic balancing (moving body). Cyclical regularity also comes into play, whether it's a single- or multi-cylinder engine.
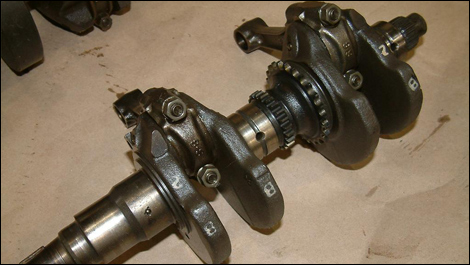 |
360-degree crankshaft |
On a two-stroke mill, the crankshaft needs to rotate a full 360 degrees to ensure complete combustion, whereas a four-stroke unit will require 720 degrees -- hence the frequency and amplitude of vibrations. This phenomenon is bad for any engine, especially a four-stroke single-cylinder.
Consequently, many engineers will choose to incorporate a balancing weight to counter vibrations and make the riding experience smoother, while ultimately reducing friction and wear. The engine will also operate more smoothly as it revs up. Of course, the addition of such a balancing device increases the overall weight and inertia. It can also affect performance substantially due to the effort required from the engine on the move.
A balancing weight is capable of neutralizing inertia entirely during the combustion cycle when the piston is at the highest point of its stroke. You should know that a general rule calls for the crankshaft to weigh the same as the connecting rod, pin and piston combined. At mid-stroke, however, a centrifugal force disrupts the balance and vibrations are peaking.
To solve this problem, the engine is fitted with one or several counterweights for the reciprocating mass of the crankshaft. These weights are actually driven by the crankshaft through a pinion-and-chain system or a gearset. Vibrations are most often felt on single-cylinder engines; in other words, cyclical regularity improves as the number of cylinders increases. That being said, the layout of the cylinders also impacts the engine operation.
 |
For example, let's take Honda's V4 engine of the early 1980s. Depending on the type of motorcycle, the manufacturer had two crankshafts: the crankpins of the first one were at 360 degrees, while those of the second one were at 180 degrees. It should be noted that the connecting rods of the pistons are mounted in pairs on the crankpins. With a 360-degree crankshaft, the piston and connecting rod assembly go up and down in parallel, producing vibrations as intense as on a single-cylinder engine. On the other hand, with a 180-degree crankshaft, the piston and connecting rod assembly operates against the opposite crankpin, which improves balance.
 |
180-degree crankshaft |
The Honda VFR800, meanwhile, uses a 90-degree four-cylinder engine. The crankshaft incorporates four pins (one for each cylinder) at an angle of 90 degrees. The resulting cyclical regularity leads to an extremely smooth, almost vibration-free operation. Motorcycle engines using horizontally-opposed cylinders are among the smoothest-running mills out there.
V-shaped engines with a single crankpin offer increased crankshaft rigidity and produce less vibrations. Others (like Honda and Yamaha) use offset crankpins at 52-, 70- or 76-degree angles. These engines are mounted on flexible rubber bushings to solve vibration transfers from the engine to the frame and rider.
An inline four-cylinder engine with a 180-degree crankshaft offers perfect balance of the primary vibrations, though secondary vibrations are still present. A simple solution is to add rubber dampers. Some manufacturers, like Kawasaki and Honda, also use a balancing shaft to prevent vibrations. Certain types of motorcycles, especially sporty models, don't have one; vibrations can thus be quite strong at specific rev spots.